Technology Overview
Technology Overview
Nanoscale carbon, such as carbon nanotubes and graphene, have exceptional mechanical and electrical properties because of their unique structure and extremely high aspect ratios (length/diameter or length/thickness). This enables them to create electrically conductive networks which are sensitive to deformation/strain. In other words, they piezoresistive.
- Our distributed sensing technique is based on leveraging these nerve-like electrical networks, which can be applied on the surface of critical areas to be monitored
- The carbon nanomaterial is deposited on a carrier fabric to create a ‘smart skin'
- Our technology can also be used in woven fabrics and non-wovens. The carrier may have a woven or non-woven structure and could be made of any material such as glass, aramid, polyester, nylon, and cotton
- The flexibility of the carrier fabric and the thin carbon nanomaterial coating enables the draping of the sensing layer onto a variety of complex geometries
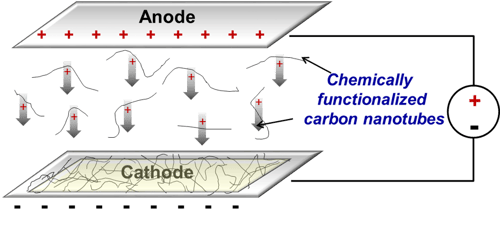
Direct Hybridization – Electrophoretic Deposition
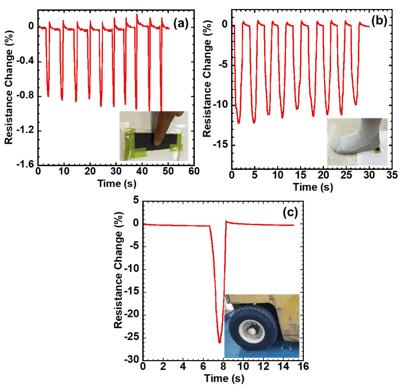
Wide Sensing Range - from Touch to Tons
Medical Sensing
Motion Sensing (Ultrahigh Sensitivity)
Highly sensitive stretch sensors are developed by coating knitted fabrics with carbon nanotubes. An innovative electrophoretic deposition approach is used to deposit a thin and conformal carbon nanotube coating on a nylon/ polyester/ spandex knitted fabric. The carbon nanotube coating is chemically bonded on the surface of the fibers and creates an electrically conductive network. As a result, these sensors display piezoresistivity, In other words, the resistance of the sensor changes due to mechanical deformation.
Motion Sensing- Upper Extremity
Pressure Detection- Walking
Structural Health Monitoring- Industrial Applications
Pressure and Damage Detection
The patented technology utilizes carbon nanotube-based coating as a thin layer (~100µm or less) on a variety of materials and surfaces.
- Non-invasive technology - no "foreign object damage“
- Potential application on surface of structure - or on mixed within polymer/rubber material
- Can be applied to metal, concrete, rubber, aramid and other materials
- Pressure sensing range from 10 kPa - 60 MPa or more
- Patented application and sensing processes
- Able to withstand repeatable bending and multiple loadings
- Can be applied to a variety of components that comprise a pipeline, junction, or other applications
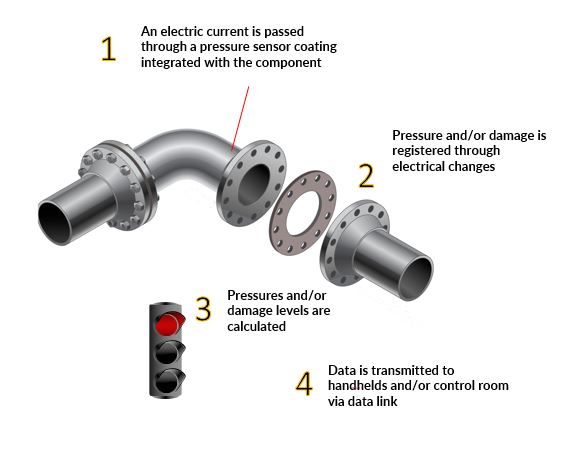
Damage Detection- High Level Overview
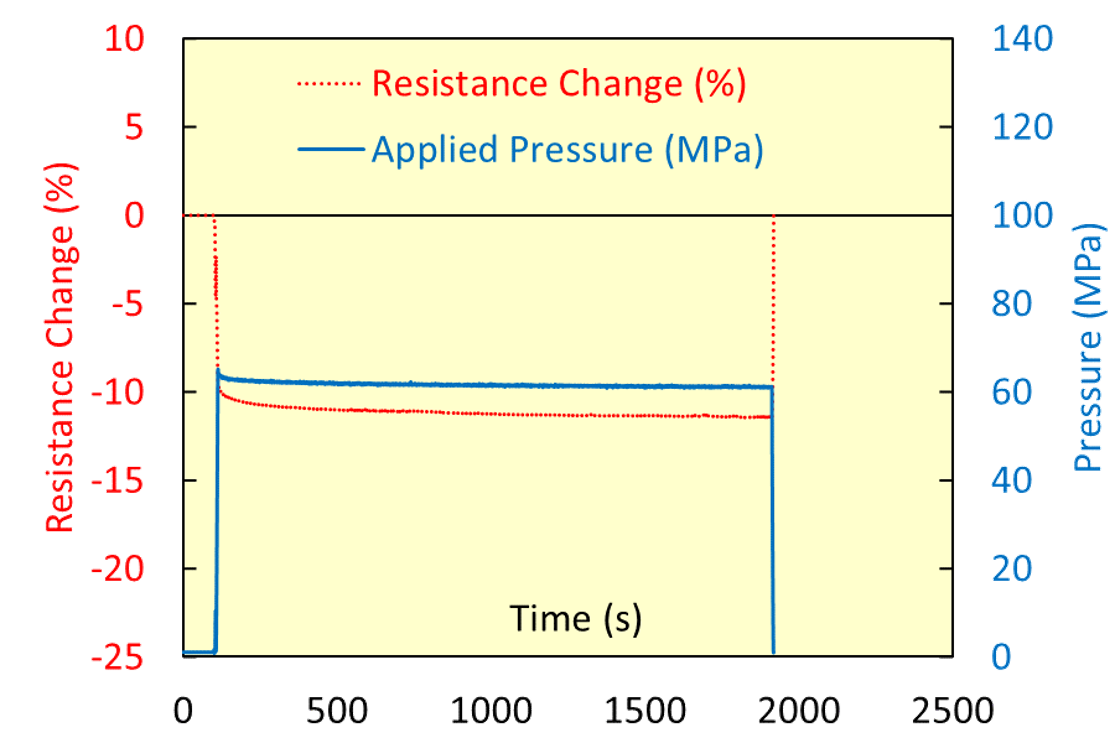
Concept Test- 30 Minute Pressure Hold
Structural Health Monitoring- Industrial Applications
Unlimited Detection Area- at any Axis
The MCET patented piezoresistive nature of the sensing network has to capability to detect mechanical deformation, damage, and/or pressure differentials.
- Non-invasive technology - no "foreign object damage“
- Can be applied to complex geometric surfaces
- Can be applied to metal or composite tanks
- Pressure sensing range from 10 kPa - 60 MPa or more
- Patented application and sensing processes
- Sensors are able to withstand repeatable bending and multiple loadings
- Can be applied to a variety of components that comprise a pipeline, junction, or other applications
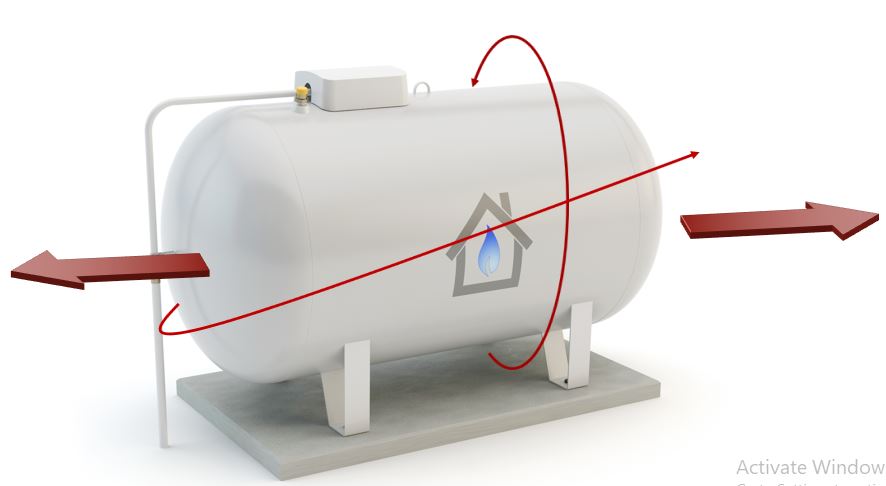
Detection Area at Any Angle- Unlimited Area
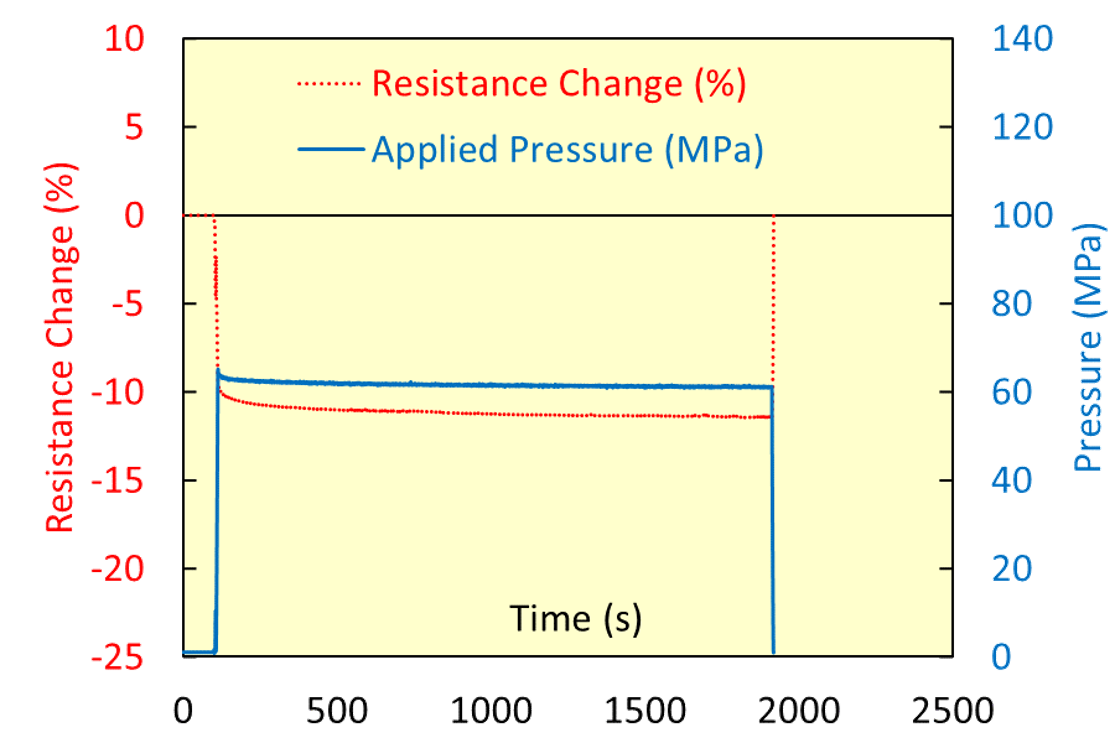
Concept Test- 30 Minute Pressure Hold
Structural Health Monitoring- Civil Engineering
Monitoring and structural repair of fatigue cracked metal structures
Metal structural components of aircraft, machines, vehicles, and infrastructure deteriorate over their service life due to static and cyclic loading, exposure to corrosive chemicals, and harsh environments. For example, steel bridges are particularly susceptible to fatigue cracking as increased traffic demands often exceed their design load capabilities and members often have fatigue-sensitive details.
- The CNT-based sensing layers can sense strain and damage and may identify the different damage, such as crack growth and debonding, by measuring conductance of its resistive network
- Tests have shown that the drilling of a traditional crack-stop hole resulted in an increase of fatigue life of only 7% while the structural/sensing composite repair increased the fatigue life by 380%
- With structural/sensing composites, the fatigue life was 534% higher
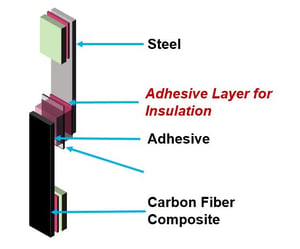
Adhesive Layer Diagram
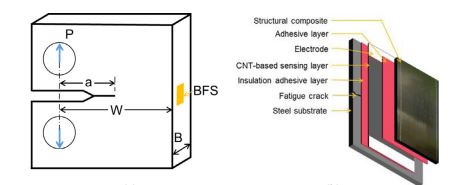
CT Specimen- CNT sensing layer for damaged steel infrastructure
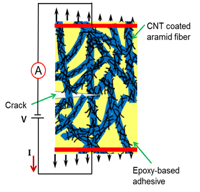